全球研发流程体系:聚集全球智慧,为智慧动力平台提供技术支撑
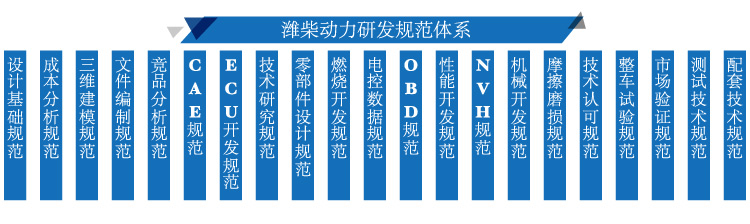
潍柴集团将进一步加大研发力度,整合“五国十地”的研发资源,以及多个“技术中心”和世界水平的产品实验室,建立完整的持续研发创新体系和成果共享,并构建一套潍柴特色的,从“模拟计算-配置优化-台架试验-整车匹配”为一体的数字化研发机制,通过数字化样机技术应用、故障机分析和虚拟实验等,在研发期排除了产品的作业缺陷,聚集全球智慧为智慧动力平台提供研发资源。
1. 三维协同设计
潍柴通过实施TOP-DOWN三维协同设计,合理高效的利用“五国十地”全球研发资源,将研发周期缩短1/3。
2. 全球零部件同步研发
与全球最具研发实力的54家零部件企业组建“潍柴动力产品研发共同体”,同步介入潍柴产品设计研发,与潍柴产品零距离匹配。
3. 整机性能开发
两大先进自动标定工具:CAMEO全智能的自适应发动机优化方案、ASCMO应用新的数据库建模方法。
标定方法:结合客户匹配情况、整车路谱采集、自主开发的应用软件,定制优化方案。
潍柴气道参数化优化设计:集成PROE三维设计、集成CFD三维流动计算。
实现燃烧室形状与气流运动和燃油喷射最优匹配,使局部过浓区域减少、温度分布更加均匀。
4. 整机可靠性开发
14项专业技术研究支撑产品可靠性提升
国内全面开展可靠性研究的机构
5. 整车优化匹配
动力总成系统(发动机+变速箱+车桥)最优匹配,动力性、经济性最强
整车道路试验(排放分析仪、油耗仪、噪声测试等车载测试设备)
整车“三高”(高温、高原、高寒)特殊环境适应性试验
6. 全程仿真计算分析
通过发动机设计仿真软件、性能仿真软件、发动机流动分析软件、动力学分析软件、有限元分析软件、疲劳分析软件等工具进行仿真计算分析。
贯穿全设计流程的仿真计算分析手段
设计、试验、仿真闭环运作,提高数据准确性
组建仿真计算集群,自主开发在线计算平台
(二)全球研发规范体系:研发标准化,最强有力的保障
800余项研发规范,满足动力总成和发动机的研发需要,支撑全球研发体系标准化运行。